
XP20 WALL & ROOF ASSEMBLIES: HIGH-PERFORANCE, LOW-CARBON SOLUTIONS
​
The XP20 Wall & Roof Assemblies are advanced vapor-open panel systems engineered for high performance, low embodied carbon, and superior moisture management. Designed to support Passive House and low-energy building strategies, these assemblies integrate wood fiber insulation, enhancing thermal performance, durability, and indoor air quality.
Through established factory partnerships, part-automation modules, and standardized detailing, Holzraum System has optimized the XP20 production process. Our decades of expertise in building science, panelized design, and precision manufacturing are available as consulting scopes to assist design teams with seamless XP20 integration. Currently, XP20 Assemblies are in production with our New York and British Columbia manufacturing partners and are being specified for residential projects across both U.S. coasts.
​
​KEY INNOVATIONS:
-
Vapor-Open Exterior Insulation – Wood fiber’s 20-perm permeability enables 2x–4x greater drying capacity than conventional sheathing.
-
Hygroscopic Moisture Buffering – Prevents mold, rot, and indoor air pollutants.
-
Thermal Storage & Phase Shift – Reduces temperature fluctuations, improving comfort.
-
Carbon Sequestration – Wood-based assemblies store COâ‚‚, reducing embodied carbon.
-
Sustainable Sourcing – PEFC-certified materials ensure responsible forestry and low environmental impact.
XP20 offers a scalable, carbon-smart solution to offsite construction, optimizing energy efficiency, resilience, and long-term durability.

A CRITICAL NEED - EXPANDED DfMA IN LOW CARBON AEC
​
Design for Manufacture and Assembly (DfMA) was initially developed to reduce production costs by optimizing components for efficient fabrication and assembly. Pioneered in the 1960s and 1970s, it gained traction in industries like aerospace and automotive manufacturing, where streamlined processes led to significant cost savings and efficiency improvements. However, the construction industry has been slower to fully embrace DfMA due to its fragmented supply chain and project-based approach. While prefabrication has integrated aspects of DfMA, its application has often been limited to discrete building components—such as modular MEP systems, panelized wall assemblies, and precast concrete—rather than whole-building solutions. As a result, optimization tends to occur within isolated trades rather than across entire projects, leaving substantial efficiency gains unrealized.
​
Holzraum System’s Single Integrated Manufacturing Model (SIMM™) expands DfMA principles to address these gaps. By integrating structural, enclosure, and interior systems into a unified manufacturing logic, SIMM optimizes fabrication, interconnection, and on-site assembly, minimizing labor, material waste, and project timelines. This systemic approach transforms DfMA into a scalable, industrialized model for precision and affordability, leveraging digital-to-factory workflows to unlock new efficiencies in construction.
A SIMM workflow, following Agile design methodologies, facilitates a linear yet iterative flow of project data, enabling continuous exchange, refinement, and feedback loops, ensuring adaptive, real-time collaboration across all project phases.
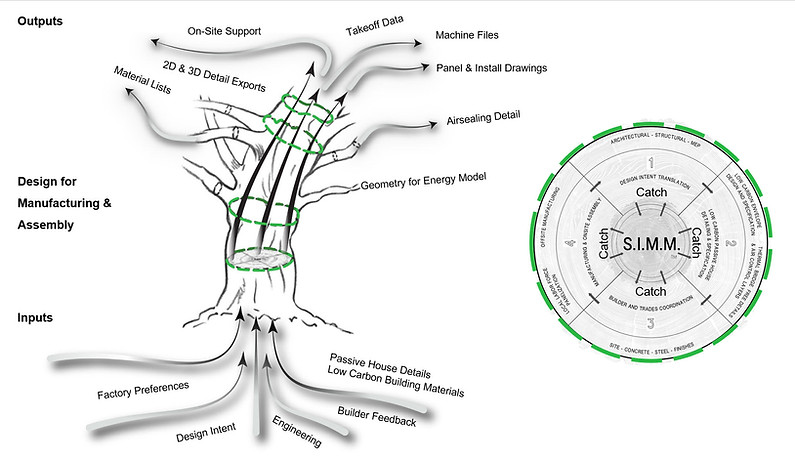
.jpg)
NUGGET 3DP - CADWORK API
​
The Nugget 3DP emerged from our need to streamline and enhance our team’s ability to navigate and communicate part and assembly relationships within complex SIMM™ models, which can contain over 40,000 data-rich parts. Initially, we developed a structured modeling protocol that enabled us to define a boundary box and clone every 3D object, surface, line, and node within those boundaries—while retaining all texture and data attribute values. This approach allowed us to generate standalone assembly models that could be updated dynamically and shared with project teams as our DfMA content evolved.
​
To integrate this process more effectively into our workflow, we collaborated with Holzraum’s in-house software development team to script Nugget 3DP as a Cadwork API. It has since become a core component of our standard design toolkit, used across both production and architectural projects.
​
Common Applications of Nugget 3DP:
-
Design & Modeling – Enhancing 3D visualization and iteration.
-
Coordination – Improving interdisciplinary collaboration.
-
Education – Supporting training and knowledge-sharing.
-
Field Support – Assisting in construction and on-site troubleshooting.
.png)
DfMA DESIGNER'S ROADMAP
​
The DfMA Designer’s Roadmap is a structured yet adaptable workflow designed to streamline digital-to-factory coordination for offsite construction projects. Borrowing from Agile Design Methodologies, it provides a linear but flexible framework, guiding novice through experienced designers in implementing DfMA (Design for Manufacture and Assembly) principles within the Single Integrated Manufacturing Model (SIMM™).
​
Currently, this roadmap is being compiled into a ClickUp and Catch toolset, incorporating:
​
-
Checklists for design intent & QC model reviews
​
-
Factory preferences workbooks
​
-
Resource links for CAD workflows and panel production
​
This digital project workbook facilitates panelized design, factory coordination, and precision manufacturing, ensuring a seamless integration of structural, enclosure, and interior systems. With embedded SIMM volumes, load path coordination, clash detection, and automated panel drawing workflows, the roadmap optimizes DfMA project delivery across multiple trades.
​
By standardizing workflows and automating key steps, this toolset enhances quality control, design efficiency, and real-time project tracking, driving the next evolution in industrialized, low-carbon construction.
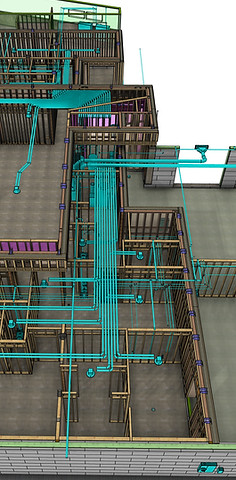
EXPANDED DfMA CURRICULUM
​
Certificate Program in Offsite & High-Performance Building Design
(DfMA & The Single Integrated Manufacturing Model – SIMM)
​
This certificate program provides a specialized pathway for students seeking expertise in offsite construction, high-performance building design, and digital fabrication. Built around Holzraum System’s Expanded DfMA framework and Single Integrated Manufacturing Model (SIMM), the curriculum explores strategies for integrating design, engineering, and production workflows to optimize efficiency and sustainability. Students will engage in advanced modeling, material efficiency, and offsite methodologies, gaining insight into the evolving landscape of industrialized construction. Through hands-on learning, they will apply cutting-edge digital tools and design strategies to bridge architecture and manufacturing.
​
Key Learning Outcomes:
-
Explore Industry Technologies – Work with specialized modeling and fabrication tools used in offsite production.
-
Advance Sustainable & High-Performance Design – Investigate building performance strategies, material selection, and energy efficiency.
-
Gain Expertise in Offsite Construction – Learn about prefabricated and modular systems optimized for streamlined production.
Capstone Project – Apply knowledge in a hands-on workshop focused on real-world applications.
This Certificate Program prepares students for careers in architectural technology, computational design, and industrialized construction, positioning them at the forefront of innovation in Expanded DfMA and sustainable building solutions.